13 Aug, 2024
What is Synthetic Fabric? 5 Differences Between Natural and Synthetic Fibers
Fabric
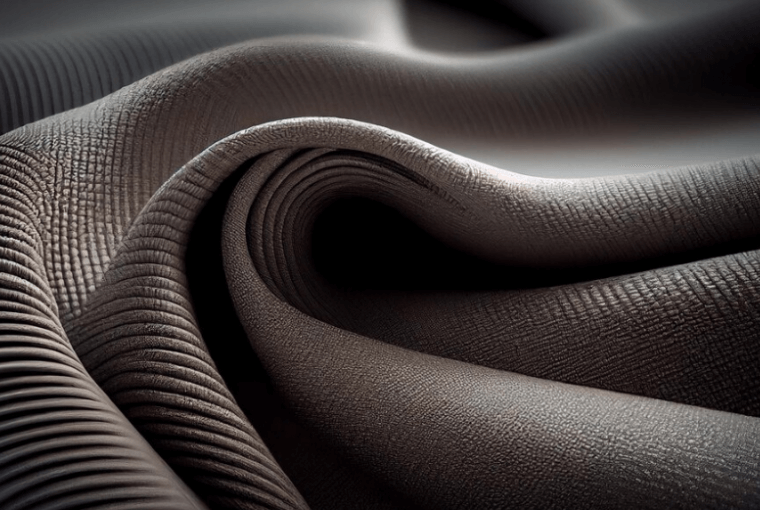
More Details
Have you ever wondered what your clothes are really made of? Synthetic fabrics have become a major part of our everyday wardrobes, but what exactly are they? In this article, we'll explore synthetic fabrics in detail and compare them with natural fibers. Let’s learn more!
Read more: What is Natural Fabric? 5 Most Common Natural Fiber Types and Textiles
What is synthetic fabric?
Synthetic fabrics are textiles made from human-created fibers, typically using petroleum-based chemicals. Unlike natural fibers like cotton or wool, synthetic fibers are engineered in labs to have specific properties. The process starts with raw materials like petroleum, which are transformed into polymers. These polymers are then spun into fibers using various methods, depending on the qualities we want in the final fabric.
Some common synthetic fabrics include:
-
Polyester: Durable, wrinkle-resistant, and quick-drying. It's everywhere, from clothes to furniture.
-
Nylon: Strong and elastic, great for activewear and outdoor gear.
-
Acrylic: Mimics wool's warmth and softness, often used in sweaters and blankets.
-
Spandex: Super stretchy, perfect for sportswear and swimsuits.
These fabrics have revolutionized the textile industry, offering solutions that natural fibers can't always provide. They're in our everyday clothes and specialized products alike. However, there's a downside: synthetic fabrics can be harsh on the environment, especially when it comes to disposal and microplastic pollution. As we continue to use these materials, finding ways to make them more sustainable is a key challenge for the industry.
Characteristics of synthetic fabrics
Synthetic fabrics possess several distinct characteristics that contribute to their widespread popularity in a variety of applications. These characteristics are the result of meticulous engineering and chemical processes that tailor the fibers to meet specific needs. Here’s a detailed look at the key attributes of synthetic fabrics:
1. Strength
One of the most notable characteristics of synthetic fabrics is their strength. Unlike natural fibers, which can vary in strength depending on their source, synthetic fibers are engineered to be consistently strong. This high strength translates into fabrics that can withstand significant stress and strain without breaking, making them ideal for applications that demand durability, such as activewear, outdoor gear, and industrial textiles.
2. Durability
Synthetic fabrics are renowned for their durability. They resist wear and tear much better than many natural fibers, which tend to degrade over time. This durability makes synthetic fabrics particularly suitable for high-stress environments where longevity is crucial. For instance, nylon is often used in products like parachutes, ropes, and high-performance sports equipment because of its exceptional durability.
3. Wrinkle resistance
Another advantageous property of synthetic fabrics is their wrinkle resistance. Unlike natural fibers like cotton or linen, which can wrinkle easily and require frequent ironing, synthetic fabrics are designed to maintain a smooth, neat appearance. This wrinkle resistance is particularly beneficial for clothing and home textiles, offering a polished look with minimal maintenance.
4. Weather resistance
Synthetic fabrics are less susceptible to damage from environmental factors such as mold, mildew, and moisture. This weather resistance makes them ideal for outdoor applications where exposure to the elements is a concern. For example, polyester is commonly used in outdoor furniture, awnings, and tents due to its ability to withstand moisture and resist mildew growth.
5. Colorfastness
Synthetic fabrics are known for their excellent colorfastness, meaning they retain their color well even after repeated washing and exposure to sunlight. This is a significant advantage over natural fibers, which can fade over time. The vibrant and long-lasting colors of synthetic fabrics make them a popular choice for fashion and home décor items that require consistent aesthetic appeal.
6. Easy maintenance
One of the most consumer-friendly characteristics of synthetic fabrics is their ease of maintenance. These fabrics are often machine washable and dry quickly, reducing the time and effort needed for care. Additionally, many synthetic fabrics are resistant to shrinking and stretching, maintaining their shape and size after washing. This easy maintenance makes synthetic fabrics a convenient option for busy individuals who prefer low-maintenance clothing and textiles.
Natural vs. synthetic fibers
Both types of fibers have unique attributes, advantages, and disadvantages that influence their applications and sustainability. We’ve created a table for you below to understand it better.
Feature | Natural Fibers | Synthetic Fibers |
---|---|---|
Source | Plants or animals | Petroleum-based chemicals |
Strength | Variable, generally lower | High |
Durability | Prone to wear and tear | Excellent |
Wrinkle Resistance | Low, wrinkles easily | High, resists wrinkles |
Moisture Absorption | High, breathable | Low, less breathable |
Environmental Impact | Renewable, biodegradable | Non-renewable, not biodegradable |
Comfort | High, soft and breathable | Lower, less breathable |
Cost | Higher, especially for premium fibers | Lower, more cost-effective |
Natural Fibers
Natural fibers come from renewable resources like plants and animals, and they’ve been a part of the textile world for centuries. Think cotton, wool, silk, and linen. These fibers are known for being comfy, breathable, and biodegradable, offering some serious perks that synthetic fibers can’t always match.
Pros
- Renewable Sources: Natural fibers come from plants like cotton and flax or animals like sheep. They’re renewable, so they help support sustainable agriculture.
- Biodegradable: Unlike synthetic fibers, natural ones break down quickly and don’t leave harmful residues behind.
- Breathability & Comfort: They’re great at regulating body temperature, making them ideal for all kinds of weather.
- Hypoallergenic: Fibers like cotton and silk are gentle on the skin, making them a solid choice for those with sensitivities or allergies.
Cons
- Durability: Natural fibers can wear out faster than synthetics, meaning they may not last as long.
- Cost: Because they require more labor to farm and harvest, natural fibers can be pricier, and the price can change depending on crop conditions.
- Maintenance: These fibers often need extra care, like regular ironing for cotton and linen or special cleaning for wool and silk.
- Environmental Impact: For instance, cotton farming uses a lot of water and can involve pesticides, although sustainable farming practices are becoming more common.
Synthetic Fibers
Synthetic fibers, like polyester, nylon, and spandex, are made from chemical compounds, mostly derived from petroleum. These fibers are engineered for specific purposes, which is why they are super versatile and widely used in all sorts of industries.
Pros
- Durability: Synthetic fibers are built to last. They’re tough and resist wear and tear, making them perfect for activewear, outdoor gear, and industrial products.
- Low Maintenance: They don’t wrinkle or shrink easily, so clothes made from them hold their shape even after many washes.
- Cost-Effective: These fibers are cheaper to produce, which helps keep prices down for consumers.
- Customizable Properties: They can be engineered with special features like stretch, water resistance, and flame retardancy, so they’re perfect for both fashion and functional uses.
Cons
- Non-Renewable Resources: Synthetic fibers are made from petroleum-based products, which raises concerns about their long-term sustainability.
- Environmental Impact: They don’t biodegrade easily, so they contribute to landfill pollution.
- Breathability Issues: Synthetic fibers trap heat and moisture, making them less comfy in hot or humid weather.
- Energy-Intensive Production: Creating these fibers uses a lot of energy and releases pollutants.
- Microplastic Pollution: When synthetic fibers are thrown away, they can break down into microplastics, which are harmful to marine life.
In short, natural fibers are great for the environment and your comfort, while synthetic fibers offer durability, low maintenance, and versatility. The right choice depends on your priorities and needs.
Natural fibers vs. synthetic fibers: pros and cons
Aspect | Natural Fibers | Synthetic Fibers |
---|---|---|
Pros |
|
|
Cons |
|
|
The classification of synthetic fibers
Synthetic fibers are engineered materials derived from petrochemical or renewable sources and are designed to exhibit specific physical properties that cater to various industrial and consumer needs. They can be classified into several categories based on their chemical structure, manufacturing processes, and distinctive characteristics.
1. Polyamide
Polyamide fibers, including nylon, polyester, elastane (spandex), and aramid fibers (such as Kevlar and Nomex), are among the most versatile and widely used synthetic fibers. The polyamide family is created through a polymerization process, where diamines and dicarboxylic acids, such as hexamethylenediamine and adipic acid, react to form strong and resilient chains of molecules. The resulting polymers have strong intermolecular hydrogen bonds, giving these fibers excellent tensile strength and abrasion resistance.
Nylon, one of the most well-known polyamide fibers, is used in a wide range of applications due to its elasticity and durability. It’s commonly found in hosiery, activewear, industrial textiles, and ropes. Elastane, another polyamide, is highly valued in activewear, swimwear, and performance fabrics because of its ability to stretch up to five times its original length while maintaining its shape. For industrial uses, aramid fibers like Kevlar are prized for their exceptional strength-to-weight ratio, making them suitable for high-performance applications such as bulletproof vests and aerospace components. Nomex, another aramid fiber, is renowned for its thermal resistance and is primarily used in flame-resistant clothing for firefighters and industrial workers exposed to extreme heat.
2. Poly-Vinyl
Poly-Vinyl fibers, such as acrylic and modacrylic, are made from polyvinyl chloride (PVC) or acrylonitrile. Acrylic fibers are synthesized by the polymerization of acrylonitrile and often contain a small percentage of other monomers to improve their processing and performance. These fibers are known for their lightweight properties, warmth, and UV resistance, which makes them excellent alternatives to natural wool. Acrylic is commonly used in sweaters, blankets, and outdoor fabrics due to its softness and warmth, while being resistant to fading and deterioration when exposed to sunlight. Additionally, modacrylic, a modified version of acrylic, contains more chlorine-based monomers and offers flame resistance, which makes it ideal for fire-resistant garments and upholstery materials.
While acrylic fibers provide good moisture resistance and are easy to dye, modacrylic fibers are often used in protective workwear and high-performance textiles because they have better flame-retardant properties compared to regular acrylic. Both fiber types are typically found in applications requiring resistance to the environment, such as outdoor gear and decorative textiles.
3. Chlorofibre
Chlorofibre fibers, such as those made from polyvinyl chloride (PVC), are synthetic fibers known for their chemical resistance, weathering resistance, and waterproof capabilities. PVC fibers are produced from the polymerization of vinyl chloride monomers. These fibers are highly durable and resistant to degradation from exposure to chemicals, oils, and environmental stressors, which makes them suitable for industrial applications. PVC fibers are used in protective clothing for workers in hazardous environments where they may be exposed to harmful substances like acids, oils, or solvents.
Moreover, chlorofibre fibers are commonly used in raincoats, shower curtains, tarpaulins, and waterproof fabrics due to their superior waterproofing properties. The material’s resistance to UV degradation makes it ideal for outdoor products. However, one of the challenges with PVC fibers is that they are non-breathable, which can limit their comfort in some applications. Despite this, their chemical stability and low cost make them ideal for many commercial products.
4. Fluorofibre
Fluorofibre fibers are a category of synthetic fibers made from fluoropolymers such as Teflon (polytetrafluoroethylene - PTFE). These fibers are made through the polymerization of tetrafluoroethylene (TFE) and are known for their exceptional resistance to heat, chemicals, and staining. The polymer backbone in fluorofibers is composed of carbon-fluorine bonds, which are highly stable, making these fibers incredibly inert and resistant to aggressive environments.
Teflon, one of the most well-known fluorofibers, has a high thermal stability, allowing it to withstand temperatures as high as 260°C (500°F) without degrading, making it ideal for high-performance applications. Fluorofibers are used in protective clothing in the aerospace industry and for industrial filtration systems, as they can endure extreme conditions without losing their integrity. The non-stick properties of Teflon also make it a preferred coating for fabrics used in non-stick protective clothing. The low surface energy of Teflon-treated fibers means that these fabrics are also resistant to dirt, water, and stains, making them ideal for specialized applications such as chemical-resistant workwear and industrial protective gear.
5. Aramid
Aramid fibers such as Kevlar and Nomex belong to a family of high-performance polyamides with aromatic rings in their molecular structure. This special configuration gives aramid fibers their exceptional strength, thermal stability, and resistance to abrasion. The unique structure of aramids allows them to withstand extreme conditions while maintaining high mechanical strength, making them critical in applications where durability and protection are required.
Kevlar, a well-known aramid fiber, is renowned for its high tensile strength, which is five times greater than that of steel by weight. As a result, it is extensively used in the production of ballistic vests, helmets, cut-resistant gloves, and automotive parts. Similarly, Nomex, another aramid, is specifically designed for high-temperature resistance and is used in flame-resistant clothing for firefighters, military personnel, and industrial workers. These fibers are also integral in aerospace applications, where both thermal protection and mechanical strength are paramount.
While both Kevlar and Nomex are prized for their strength and heat resistance, aramid fibers can be challenging to process due to their high melting points and low wettability with common solvents, which requires specialized techniques during manufacturing. Their integration into textiles, however, is crucial in enhancing safety and performance in extreme environments.
How are synthetic fibers made?
Synthetic fibers are engineered materials that are produced through complex chemical processes designed to transform raw materials into fibers with specific properties such as strength, flexibility, and moisture resistance. The production of synthetic fibers is highly technical, and the entire process involves several intricate stages. Understanding the specifics of each step is crucial for anyone working with textiles, especially when it comes to adjusting properties for specialized applications. Here's an in-depth look at how synthetic fibers are made:
1. Sourcing Raw Materials
The production of synthetic fibers begins with the extraction of raw materials, primarily from petrochemicals. The most common raw materials are derived from crude oil, natural gas, and coal, which are processed into monomers — the basic building blocks of polymers. In the case of synthetic fibers like polyester and nylon, these monomers are typically hydrocarbons like ethylene (from petroleum) or caprolactam (from coal). The quality of the raw materials is essential because the molecular structure of the monomers will influence the properties of the resulting fibers, such as their strength, durability, and elasticity.
For example, in polyester production, ethylene glycol and terephthalic acid are the main monomers derived from petrochemical refining. These two compounds are used to create the polyester polymer that is spun into fiber form. Similarly, nylon starts with hexamethylenediamine and adipic acid, both derived from crude oil and natural gas.
2. Polymerization
Once the monomers are sourced, they undergo polymerization, a chemical process that links the monomers into polymers—long chains of repeating molecular units. The type of polymerization depends on the fiber being produced, and there are two primary methods used:
-
Addition Polymerization: In this method, monomers like propylene and ethylene are chemically bonded to form long chains without the byproducts of other chemicals. This process is often used to make fibers such as polypropylene and polyethylene. It results in a simpler structure, which gives these fibers excellent resilience and moisture-wicking properties.
-
Condensation Polymerization: This method is used to create more complex structures such as nylon and polyester, where byproducts like water or methanol are released during polymerization. This allows for greater control over the molecular structure, which can impact the fiber’s strength, flexibility, and thermal stability. Nylon, for example, is created by polymerizing hexamethylenediamine and adipic acid to form long chains of polyamide molecules.
3. Melting or Dissolving the Polymer
Once polymerization is complete, the resulting polymer is processed to prepare it for fiber production. Depending on the type of fiber, the polymer will either be melted or dissolved into a solution:
-
Melting: For fibers like polyester and nylon, the polymer is heated to its melting point, where it turns into a viscous liquid. The molten polymer is then ready to be extruded through a spinneret to form fibers. The melting point plays a crucial role in fiber properties, such as heat resistance and durability.
-
Dissolving: For fibers like acrylic, acetate, or spandex, the polymer is dissolved into a solvent (such as dimethylformamide or acetone) to form a viscous solution. The solvent allows the polymer to be processed at lower temperatures than melting, which is particularly beneficial for delicate fibers or those that need specific treatments like dyeing or coating.
4. Spinning the Fibers
The polymer solution or melt is then extruded through a device called a spinneret, which is a metal plate with tiny holes resembling a showerhead. The size and shape of these holes determine the diameter, texture, and characteristics of the resulting fiber. There are three primary spinning methods, each suited to different types of synthetic fibers:
-
Melt Spinning: Used for fibers like polyester and nylon, where the polymer is melted and forced through the spinneret. As the polymer cools, it solidifies into long, continuous fibers. Melt spinning is favored for its efficiency and the ability to create fine denier fibers with consistent thickness and strength.
-
Dry Spinning: This method is used for fibers like acetate and acrylic. The polymer is dissolved in a solvent and extruded through the spinneret. The solvent evaporates in a hot air stream, leaving behind solid fibers. This process is slower than melt spinning but allows for the creation of lighter, more delicate fibers.
-
Wet Spinning: Used for fibers like rayon, where the polymer is extruded into a coagulating bath of chemicals that solidify the fiber. Wet spinning is ideal for fibers that need to undergo further chemical treatments before they can be used in textiles.
5. Drawing and Stretching
After the fibers have been spun, they are drawn or stretched to align the polymer chains. This step is crucial for increasing the strength and elasticity of the fibers. By stretching the fibers, the polymer chains become more oriented in a parallel direction, which enhances the fiber’s tensile strength and uniformity in diameter. This process also improves the fiber's elasticity, which is especially important for materials like elastane (spandex), which need to maintain their stretchability over repeated use.
6. Texturizing and Finishing
Once the fibers are drawn, they are often texturized to enhance specific properties, such as softness, bulkiness, or elasticity. This is especially important for fibers that will be used in apparel or home textiles, where tactile properties are crucial. Texturizing involves using heat or mechanical processes to create loops, crimp, or twist in the fibers, which can increase their bulk or alter their surface texture.
During the finishing stage, additional treatments are applied to the fibers, such as dyeing, water repellents, or flame retardants. Finishing processes are tailored to meet the performance requirements of the final textile product, whether for activewear, outdoor gear, or industrial fabrics.
7. Weaving or Knitting into Fabrics
The final step in synthetic fiber production involves weaving or knitting the fibers into yarns, which are then used to create fabrics. The choice between weaving (interlacing threads in a crisscross pattern) and knitting (interlooping threads) depends on the intended use of the fabric. Woven fabrics tend to be stiffer and more durable, while knitted fabrics are more elastic and stretchable. Once the fabric is produced, it can be used for a wide range of applications, from clothing to industrial textiles, depending on the fiber’s characteristics.
These stages of synthetic fiber production involve a high level of precision and control. By adjusting factors such as polymerization methods, spinning techniques, and drawing processes, manufacturers can tailor the properties of synthetic fibers to meet the specific demands of diverse industries, from fashion to aerospace.
What Fabrics Are Synthetic?
Synthetic fabrics are man-made materials designed to mimic or enhance the properties of natural fibers. Unlike natural fibers, which are derived from plants or animals, synthetic fibers are created using chemical processes that typically involve petroleum-based raw materials. While the production methods for synthetic fibers vary, they are all engineered to offer specific characteristics such as durability, elasticity, and moisture resistance. Let’s dive into some of the most common types of synthetic fabrics and what makes them unique.
1. Polyester
Polyester is one of the most widely used synthetic fabrics, and its popularity is a direct result of its durability, wrinkle resistance, and low-maintenance properties. It is made from polyethylene terephthalate (PET), a polymer derived from petroleum-based products. The manufacturing process involves polymerization, where the raw materials are chemically bonded to form long chains of molecules. Polyester is incredibly strong, resistant to abrasion, and holds its shape well, making it ideal for clothing, upholstery, and industrial applications. A key feature of polyester is its hydrophobic nature, meaning it does not absorb moisture, making it dry faster than natural fibers. This makes polyester a popular choice for activewear and outdoor gear.
Moreover, recycled polyester (rPET) is gaining traction as a sustainable alternative, produced by repurposing post-consumer PET plastic bottles, reducing the environmental impact and promoting circular economy practices.
Is polyester a synthetic fiber?
Yes, polyester is definitely a synthetic fiber! It’s one of the most commonly used materials in the textile industry, and it’s made through a chemical process that uses petroleum-based products. Here’s a breakdown of how it works:
Why polyester is considered a synthetic fiber?
- Chemical Composition: Polyester is made from polymers, specifically polyethylene terephthalate (PET), which comes from petroleum. The whole production process involves chemical reactions, including polymerization, to create long chains of synthetic molecules.
- Man-Made Process: Unlike natural fibers like cotton or wool, which come from plants or animals, polyester is completely man-made. It’s created in labs or factories, so it’s the perfect example of a synthetic fiber.
2. Nylon
Nylon, the first fully synthetic fiber created in the 1930s, is known for its strength and elasticity. Unlike polyester, which is derived from polyethylene terephthalate (PET), nylon is made from polyamide polymers, which are synthesized through condensation polymerization using hexamethylenediamine and adipic acid. This polymer structure imparts exceptional tensile strength, making nylon ideal for activewear, hosiery, swimwear, and industrial products such as ropes and parachutes.
Nylon is also highly resistant to wear and tear, abrasion, and stretching, and it is lightweight and smooth to the touch. Its moisture-wicking properties make it particularly suitable for performance fabrics, but it is also susceptible to yellowing and damage from sunlight due to the lack of UV resistance in standard nylon.
3. Acrylic
Acrylic fibers were developed to mimic the qualities of wool, offering a lightweight, warm, and soft alternative. Acrylic is produced by polymerizing acrylonitrile and can be made into fibers that resemble natural wool in texture. Acrylic fibers are resistant to UV light, which makes them ideal for outdoor applications like blankets, sweaters, and furniture upholstery. Unlike natural wool, acrylic does not retain moisture, making it quick-drying and resistant to mildew and mold.
The key to acrylic’s functionality lies in its ability to maintain colorfastness and resist sunlight degradation, which is why it is a popular choice for outdoor furniture and sun-protection fabrics. However, acrylic is prone to pilling, which can affect its appearance over time.
4. Spandex (Lycra or Elastane)
Spandex, also known by its brand name Lycra, is one of the most elastic synthetic fibers, capable of stretching up to five times its original length. Made from polyurethane-based polymers, spandex is often blended with other fibers to add stretchability and flexibility to fabrics. This makes it indispensable in activewear, swimwear, and form-fitting clothing like leggings and sports bras.
Spandex’s elasticity provides excellent shape retention, allowing garments to return to their original form after being stretched. It also has a low moisture absorption rate, which helps in reducing sweat retention in performance apparel. However, spandex can degrade over time when exposed to chlorine in swimming pools, and it is sensitive to heat.
5. Rayon (Viscose)
Rayon is a semi-synthetic fiber, meaning it is derived from natural cellulose but undergoes extensive chemical processing. It is made from materials like wood pulp, cotton linters, or bamboo that are processed using chemicals such as sodium hydroxide and carbon disulfide to produce the fiber. Rayon has a luxurious feel and drape that resembles natural fibers like silk and cotton, which is why it’s often used in clothing, upholstery, and industrial products.
Despite its natural origins, rayon is classified as semi-synthetic because it requires significant chemical treatment to transform cellulose into the fiber form. Rayon fabrics are often soft, breathable, and comfortable to wear, but they lose strength when wet and can wrinkle easily. The production of rayon raises environmental concerns, particularly with the chemical treatment of cellulose, although newer methods like lyocell (also known as Tencel) aim to provide a more sustainable alternative.
Is rayon a synthetic fiber?
Rayon is technically considered a semi-synthetic fiber, not a fully synthetic one. While it comes from natural materials like wood pulp or plant-based cellulose, the process used to turn those materials into rayon involves a fair amount of chemical treatment, which is why it’s classified as semi-synthetic.
Why Rayon is Semi-Synthetic:
-
Natural Origins: Rayon starts with cellulose, which is a natural substance found in plants like wood, cotton, or bamboo. So, it has a natural base.
-
Chemical Processing: To make rayon, the cellulose undergoes a chemical process where it’s dissolved in chemicals like sodium hydroxide and carbon disulfide. This sets rayon apart from fibers like cotton or linen, which don’t require as much chemical intervention.
So, rayon is in a unique category as a fiber that’s both plant-based and chemically processed, earning it the classification of semi-synthetic.
6. Polypropylene
Polypropylene is a thermoplastic polymer that is used to make lightweight, water-resistant fabrics. It is produced through the polymerization of propylene monomers derived from petroleum. This fiber is known for its moisture-wicking properties, low thermal conductivity, and high resistance to mildew and UV light.
Polypropylene fabrics are often used in activewear, reusable shopping bags, and upholstery, thanks to their lightweight and durable qualities. The fiber is also frequently used in nonwoven fabrics for products like diapers, wipes, and filtering materials. One of its unique features is that it is resistant to chemicals and remains stable in highly alkaline environments, making it ideal for use in industrial applications as well.
7. Acetate
Acetate is a semi-synthetic fiber derived from cellulose acetate, a compound created by treating natural cellulose with acetic acid. Although it originates from a natural substance (wood pulp), the production of acetate involves significant chemical intervention, thus classifying it as semi-synthetic. Acetate fabrics are known for their silk-like appearance, smooth texture, and shiny finish, which is why they are commonly used in formal wear, linings, and home furnishings.
Despite its luxurious appearance, acetate is prone to heat sensitivity, abrasion, and water damage. It also has poor durability compared to other fibers like polyester, which limits its use to lesser-wear applications.
8. Kevlar and Nomex
Both Kevlar and Nomex are high-performance aramid fibers designed for use in demanding environments. Kevlar, known for its extreme strength and light weight, is used in ballistic vests, cut-resistant gloves, and rope. It is a polyamide fiber that has an aromatic structure, which contributes to its exceptional strength-to-weight ratio. Kevlar is ideal for protective gear, as it can withstand high amounts of stress and is resistant to abrasion and cutting.
Nomex, another aramid fiber, is engineered for flame resistance and high-temperature stability, making it suitable for use in fire-resistant clothing, protective suits for industrial workers, and aerospace components. Both of these fibers maintain their integrity under extreme conditions, making them indispensable for industries requiring high-performance textiles.
9. Microfiber
Microfiber is made from extremely fine synthetic fibers, often polyester or nylon, that are finer than a human hair. The fibers are split during production to create a fabric with a large surface area and high absorbency. Microfiber fabrics are incredibly durable, lightweight, and resistant to wear and tear, which makes them ideal for use in cleaning products, sportswear, and upholstery.
Due to its high surface area, microfiber is highly absorbent and effective at trapping dirt, which is why it is commonly used in cleaning cloths and mops. It also performs well in moisture-wicking activewear, providing quick-drying properties for sports fabrics and athleisure. The fine structure of microfiber also enables it to be woven into fabrics with a smooth finish, making it popular for luxurious-feeling products such as microfiber towels and high-end upholstery.
Is linen a natural or synthetic fiber?
Linen is classified as a natural fiber, and it is one of the oldest and most eco-friendly materials in the textile industry. Derived from the stalks of the flax plant (Linum usitatissimum), linen stands out for its minimal processing compared to other fibers. It is harvested from the plant’s stalks and goes through a process known as retting, which breaks down the plant’s outer layers to release the cellulose fibers. Unlike synthetic fibers, which are man-made from petrochemicals, linen is primarily made from renewable plant-based materials, so it's a more sustainable option.
The key factors that make linen a natural fiber are its plant-based origin, its biodegradability, and the eco-friendly processing methods involved. Linen’s processing does not require the heavy chemical treatments that synthetic fibers undergo, and it relies on water or mechanical methods during retting, minimizing environmental impact. Its breathability and lightweight nature make it especially suited for warm-weather clothing, as it naturally wicks away moisture and promotes airflow, keeping the wearer cool and comfortable. Also, linen is known for its durability. It’s one of the strongest natural fibers, and with each wash, it becomes softer and more comfortable. This combination of environmental benefits and functional properties makes linen a choice material for the sustainable fashion industry.
What Makes Linen a Natural Fiber?
1. Plant-Based Origin
Linen comes from the flax plant, which is a renewable resource that’s surprisingly low-maintenance. It needs less water and fewer pesticides to grow compared to something like cotton, making it a more sustainable option.
2. Biodegradability
Being a natural fiber means linen is biodegradable. And that’s a win for the environment. It breaks down naturally without leaving behind any nasty chemicals.
3. Eco-Friendly Processing
The process of extracting linen fibers, known as retting, is done using water or mechanical methods, which means hardly any chemicals are involved. That’s a huge plus compared to synthetic fibers, which require a lot of chemical processing.
4. Breathable and Lightweight
Linen is super breathable and does an amazing job at wicking away moisture. That’s why you’ll see it all over summer wardrobes because it keeps you cool without feeling heavy!
5. Durability
Here’s the best part: linen is one of the strongest natural fibers out there. It lasts forever, and actually gets softer and more comfortable the more you wash it.
Why Linen Isn’t Synthetic
Synthetic fibers like polyester and nylon are man-made, created through chemical processes using petroleum-based materials. Linen is the opposite. It’s a plant-based fiber that’s processed naturally, with minimal intervention, which is why it’s firmly in the "natural fiber" camp.
If you’re looking for something that’s sustainable, versatile, and just downright classy, linen is where it’s at. It’s perfect for anyone who cares about comfort and the environment... and honestly who doesn’t?
Are recycled synthetic fibers really sustainable?
Recycled synthetic fibers, like those made from recycled polyester (rPET) or nylon, are definitely a step up in sustainability compared to their virgin versions, but they come with their own set of challenges. On the bright side, recycling these fibers helps cut down on waste by repurposing things like plastic bottles and old textiles that might otherwise end up in landfills or floating around in our oceans. The process also uses less energy and water than creating new synthetic fibers from scratch, plus it lowers the demand for fossil fuels.
But let’s be real. Recycled synthetic fibers aren’t perfect. They still shed microplastics when washed, which can end up polluting our waterways. And even though recycling gives plastic a longer life, these fibers still don’t break down naturally, meaning they stick around in the environment for a really long time. So, while recycled synthetics are definitely better than the alternative, they’re not entirely guilt-free, and we’ve still got work to do to make them truly eco-friendly.
Read more: Sustainable Fabrics: How Eco-Friendly Are They Really?
How to dye synthetic fabric?
Dyeing synthetic fabrics requires specialized techniques due to their chemical composition, as these fibers do not absorb dyes as readily as natural fibers. The most common dyes used for synthetic fibers are disperse dyes, which are designed to bond with the synthetic polymer molecules. Here’s a detailed breakdown of how to dye synthetic fabrics:
1. Preparation
The first step is to clean the fabric to remove any finishes or impurities. Synthetic fibers often have a scouring process to eliminate oils and other contaminants that could affect dye adhesion.
2. Dye Bath
A dye bath is prepared by dissolving the disperse dye in water. The dyeing process requires precise measurement and adjustment of the dye-to-fabric ratio, as synthetic fibers tend to have a low affinity for dyes.
3. Heat
Different synthetic fibers require different temperatures for the dyeing process. For nylon, the dye bath is usually heated to around 140-194°F (60-90°C), as nylon is a polyamide and requires a moderate temperature to absorb the dye. On the other hand, polyester fabrics need a higher temperature—between 248-284°F (120-140°C)—to allow the dye molecules to penetrate the polymer structure. The high heat is necessary to help the dye particles bond with the hydrophobic polyester.
4. Immersion
The fabric is then immersed in the dye bath, and it is continuously stirred to ensure even dyeing. This step can take anywhere from 30 minutes to several hours, depending on the desired depth of color and type of fabric.
5. Rinse and Dry
After dyeing, the fabric must be thoroughly rinsed to remove any excess dye, preventing it from bleeding during future washes. The fabric is then dried, typically through air drying or machine drying, depending on the type of fiber.
The challenge with synthetic fabrics lies in the high temperatures required for dyeing and the need for specialized dyes. It’s important to note that synthetic fibers like polyester and nylon can have difficulty achieving certain shades compared to natural fibers like cotton, due to their lack of dye absorption properties.
Brief History of Synthetic Fabrics
The history of synthetic fabrics dates back to the early 20th century, marked by groundbreaking innovations:
1935: Invention of Nylon
The first fully synthetic fiber, nylon, was created by Wallace Carothers and his team at DuPont. This breakthrough was monumental as nylon was the first fiber made entirely from petroleum-based chemicals, specifically from polyamide polymers. Nylon’s strength, elasticity, and wear resistance made it an instant success in textiles, particularly for women's stockings and military applications during World War II.
1940s: Commercial Production of Polyester
The 1940s saw the development of polyester, another revolutionary material that would change the textile industry. The polyester fabric was durable, wrinkle-resistant, and easy to care for, making it a popular choice for clothing, upholstery, and home textiles. The development of polyester blends, which combine polyester with other fibers like cotton, further boosted its popularity due to its affordability and low-maintenance qualities.
1950s: Introduction of Acrylic and Spandex Fibers
The 1950s introduced two important synthetic fibers, which are acrylic and spandex. Acrylic provided a lightweight, warm alternative to wool, offering softness and ease of care, which made it a favorite for sweaters and blankets. On the other hand, spandex revolutionized the fashion industry with its ability to stretch up to five times its original length, making it ideal for activewear, swimwear, and athletic gear.
1960s: Development of High-Performance Fibers
The 1960s witnessed the development of aramid fibers like Kevlar and Nomex, which are known for their extreme strength and heat resistance. Kevlar, for example, is used in bulletproof vests and industrial ropes, while Nomex is favored in flame-resistant clothing.
Recent Developments: Innovations in Sustainability
The past decade has seen an increased focus on sustainable synthetic fibers. Innovations like bio-based polyester and recycled polyester (rPET) aim to reduce the environmental impact of fiber production. Companies are also exploring closed-loop recycling methods, where synthetic fibers can be continuously reused to create new textiles, reducing the need for virgin materials and the environmental footprint of textile production.
FAQs
1. What are 5 synthetic fibers?
Polyester, nylon, acrylic, spandex, and rayon.
2. What is the most popular synthetic material?
Polyester, due to its durability and versatility.
3. How can you tell if a material is synthetic?
Synthetic materials are usually smoother, less breathable, and have a uniform appearance compared to natural fibers.
4. Is denim natural or synthetic?
Traditional denim is made from cotton, a natural fiber, but can be blended with synthetic fibers for added stretch.
5. Is polyester synthetic?
Yes, polyester is a synthetic fiber made from petroleum-based chemicals.
6. What is the best dye for synthetic fabric?
Synthetic fibers require different dyes depending on the type of fabric. Disperse dyes are mainly used for polyester, but they are not necessarily the best choice for all synthetic fibers.
For specific synthetic fibers:
- Polyester: Disperse dye is the go-to choice, often used in high-temperature dye baths.
- Nylon: Acid dyes are commonly used for nylon, as they bond well with the amine groups in the fiber.
- Acrylic: Basic dyes (also known as cationic dyes) are typically used for dyeing acrylic fibers, as they provide good color fastness and bright hues.
7. What are the 4 synthetic dyes?
The four main types of synthetic dyes are:
-
Disperse Dyes: Primarily used for dyeing synthetic fibers like polyester, acetate, and nylon. These dyes are water-insoluble and are finely dispersed in the dye bath, where they attach to the fibers through heat.
-
Acid Dyes: Water-soluble dyes that are typically used on synthetic fibers like nylon and some types of acrylics. They are also used for dyeing natural fibers like wool and silk.
-
Basic (Cationic) Dyes: These dyes carry a positive charge and are mainly used for dyeing acrylic fibers, as well as other synthetic fibers that have anionic (negative) groups.
-
Reactive Dyes: While commonly used for natural fibers like cotton, reactive dyes can also be used on certain synthetic fibers like nylon. They form a covalent bond with the fiber, making the dye very wash-fast and durable.
8. Is synthetic fabric good?
Synthetic fabrics offer durability, wrinkle resistance, and cost-effectiveness but have environmental drawbacks.
9. Which is better cotton or synthetic?
It depends on the application. Cotton is more comfortable and eco-friendly, while synthetic fibers offer durability and performance benefits.
10. What are the disadvantages of synthetic fabric?
Non-biodegradable, less breathable, and potential environmental impact from production and disposal.